The pallet and strut bracket mounting is complete, and all welds have been smoothed out on the pallet. This is the most important milestone in the completion of the project. The pallet and struts for the Orion capsule medium fidelity mockup will be ready to deliver to NASA before too long! However, some minor details remain, such as performing dye-penetration testing on the welds, sand-blasting the pallet, and painting the pallet and struts.
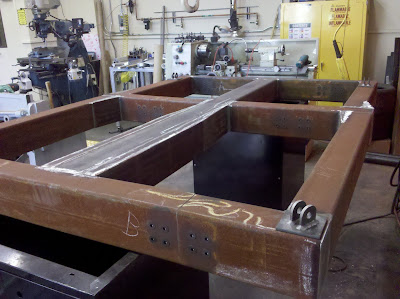 |
The pallet with vertical strut connection brackets welded to the pallet. |
This figure shows a detail of welds that have been ground flush with the surface. It is important to remember that when a weld is done properly, it is as strong as (or sometimes stronger) than the base materials that are being welded together.
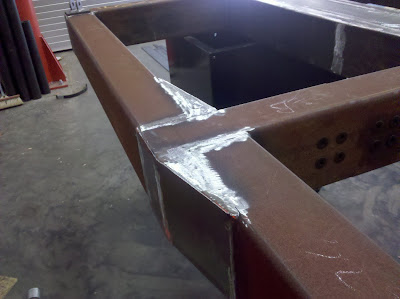 |
Detail of welds after smoothing. |
Below is another full-length view of the pallet. Recall that it will be sandblasted (to clean off all debris) and painted before delivery at NASA Johnson.
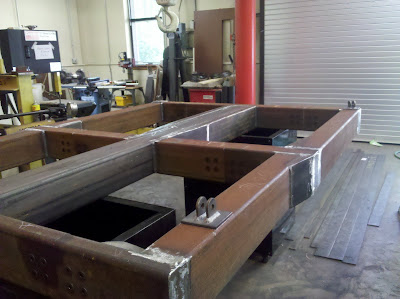 |
Another full view of the pallet. |
This figure focuses on the center portion of the pallet, where changes in width were required to insure that the overall pallet dimensions were the same as the Lockheed Martin flight design.
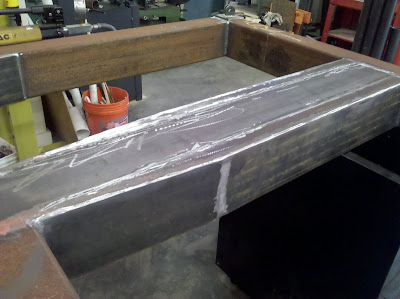 |
Close-up view of the center of the pallet. |
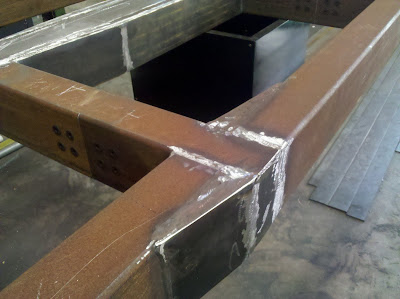 |
Close-up of another weld. |
And finally . . . Jim Mills used 3 lbs worth of grinding disks to smooth out the welds! The figure below shows what is left of them!
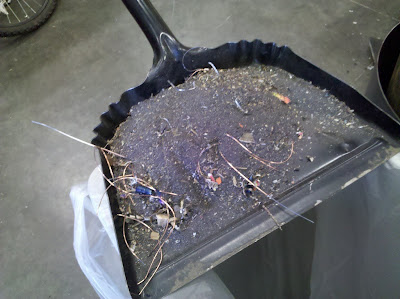 |
What's left of 3 lbs of grinding disks and smoothed welds! |